Uma das maiores dificuldades na transformação lean de uma empresa é convencer as pessoas de que trabalhar em fluxo é melhor do que trabalhar em lote. Percebemos que, quando a pessoa trabalha em lote, ela tem a falsa sensação de que está sendo mais produtiva em seu trabalho. No entanto, a realidade é que, ao realizar o trabalho em lote, ela acaba gerando esperas pelo lote. Isso significa que, ao realizar uma atividade no produto, ele fica aguardando a produção dos demais antes de ser movido para a próxima etapa. Do ponto de vista desse produto, ocorre uma espera desnecessária, pois ele poderia ser processado pela etapa seguinte mais cedo.
Outro desperdício gerado é o estoque entre processos, uma vez que a etapa que está sendo realizada gera estoque de peças entre as etapas, aguardando a conclusão do lote em produção. Isso pode levar a retrabalhos mais graves, pois um erro pode ser percebido apenas na atividade seguinte, afetando todo o lote, que precisará ser revisado e retrabalhado.
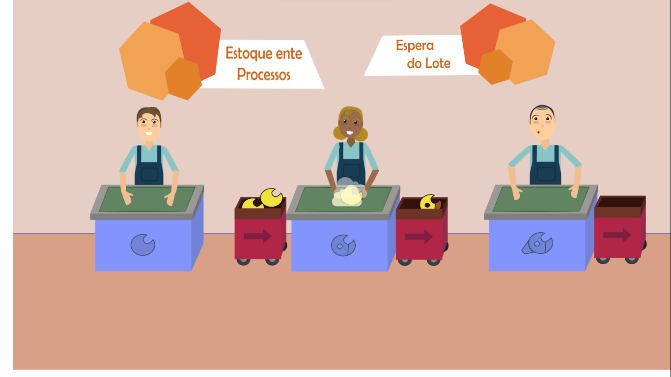
Figura trabalhando em lote
Uma das ferramentas que utilizamos para desenvolver o fluxo contínuo é o GBO (Gráfico de Balanceamento de Operadores, também conhecido como Yamazumi). Esse gráfico mostra como o trabalho é distribuído e pode ajudar a equilibrar o fluxo de trabalho. Abaixo segue um exemplo:
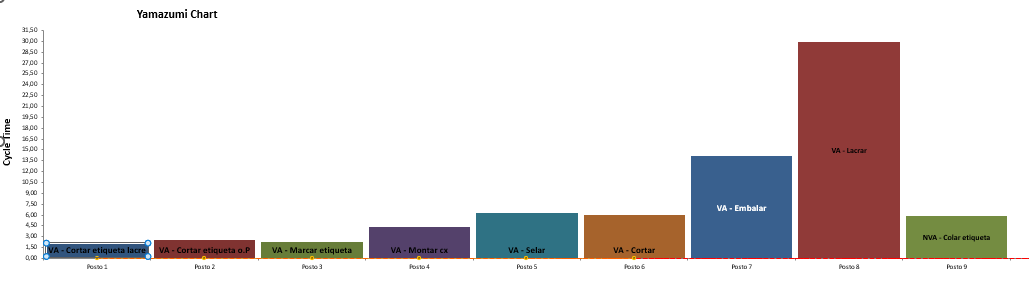
A partir desse levantamento de tempos, identificamos que seria possível implementar o fluxo contínuo na montagem final. Anteriormente, o operador realizava cada etapa em lote, levando 4,7 horas para concluir um lote de 100 peças.
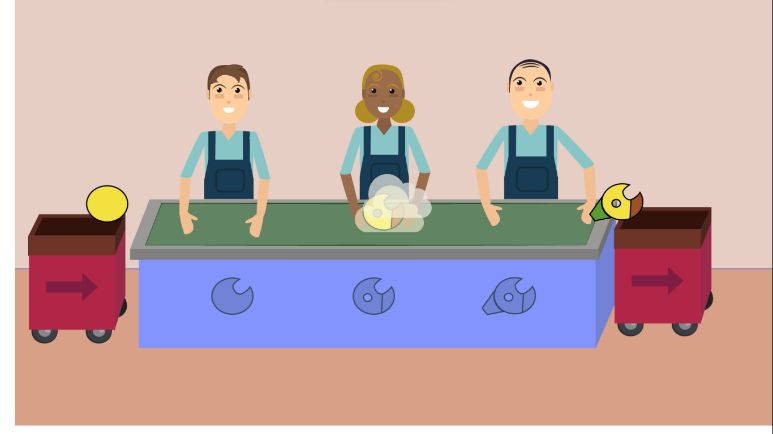
Figura de Fluxo Contínuo
Para viabilizar o fluxo contínuo, reorganizamos as atividades de forma que os tempos de cada operador ficassem próximos. Isso permitiu que o operador 1 realizasse as atividades e disponibilizasse a peça para o segundo operador. Com essa distribuição, o GBO ficou assim:
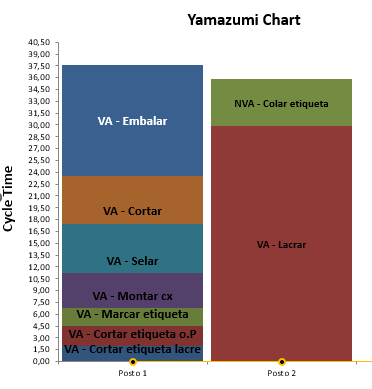
Novo GBO
Para convencer os operadores de que essa estratégia aceleraria a produção, realizamos uma dinâmica com aviões de papel. Primeiro, fizemos em lote e medimos o tempo total; depois, fizemos em fluxo, demonstrando um ganho de 40% no tempo. Com essa experiência, as pessoas passaram a acreditar na viabilidade do fluxo contínuo.
Redimensionamos o leiaute para favorecer o fluxo contínuo, utilizando mesas menores e suportes para os materiais necessários. A implementação exigiu acompanhamento hora a hora para garantir que o fluxo fosse seguido.
Após a implementação desse processo, o tempo total para processar um lote de 100 peças diminuiu de 4,7 horas para 2,8 horas, representando um ganho de produtividade de 40%. Com essa iniciativa, conseguimos reduzir praticamente um turno de trabalho. O interessante foi que, após alguns dias trabalhando em fluxo, as pessoas não queriam mais voltar a trabalhar em lote.
Se você quiser aplicar esse conceito de estudo do GBO, use o arquivo: arquivo GBO para que você possa balancear suas operações.
Caso precise de ajuda, pode contar conosco em www.2blean.com.br.
Atenciosamente,
Alexandre Cardoso
CEO da 2blean