É muito comum realizar projetos nos fluxos produtivos em processos contínuos, onde as operações individualmente apresentam boa produtividade, mas no fim do dia entregam a produção abaixo da meta.
O primeiro passo foi entender o estado atual deste processo, que era composto por 3 etapas conforme abaixo:
- Processo de mistura das matérias-primas.
- Processo de envase em um IBC de 1000 litros.
- Processo de retirada do IBC cheio e reposição com IBC vazio.
O time local já havia realizado várias melhorias, mas a produção final diária continuava baixa. Na prática, no fim do dia, o tempo médio encontrado para produção era de 22:30 minutos por IBC considerando os três operadores. Este tempo impactava em atraso na entrega para o cliente e horas extras.
Análise inicial do processo e estado futuro I
O primeiro passo foi analisar o tempo médio baseado na forma de trabalho atual, onde foram medidas as operações de envase e reposição/troca dos IBCs com uma empilhadeira dedicada, obtendo-se 9:00 minutos para envasar cada IBC para um operador. Isso confirmou que havia capacidade para melhorar a produção diária. Porém, com as análises realizadas ao longo da semana, encontrou-se vários problemas que impactavam no fluxo e ritmo produtivo adequado. Os principais pontos para melhorar foram listados abaixo:
- Horário de trabalho do operador de mistura de matéria-prima era diferente dos horários de entrada, saída e refeições das operações de envase e troca de IBC.
- O operador que efetuava o envase precisava frequentemente procurar a empilhadeira para troca de IBC, que estava ocupada com outras atividades em outras operações.
- Falta de matérias-primas e ferramentas de trabalho ao longo do fluxo, impactando pequenas paradas no fluxo.
- Falta de sincronização e conexão entre operações e reorganização das atividades.
Com isso, foi realizada uma simulação no processo considerando um operador fixo no envase e um operador fixo manuseando os IBCs com empilhadeira. Organizando as operações, foi obtido o tempo de 5:35 minutos para cada IBC. Também foi revisto o alinhamento de horário entre operações e definido o horário de trabalho das 3 operações no mesmo horário, conseguindo assim garantir o ritmo produtivo de 5:35 para as 3 operações.
Estado futuro II
Observou-se que havia dois pontos de envase, mas a operação usava cada ponto de envase somente para famílias específicas de produtos. Com o objetivo de reduzir o tempo de setup, foi realizado um pequeno investimento que possibilitou que ambos os pontos pudessem ser utilizados simultaneamente para qualquer família, com um único operador atuando neste local, possibilitando envasar em 2 pontos de envase. Com isso, foi obtido o novo tempo de operação de 4:30 segundos.
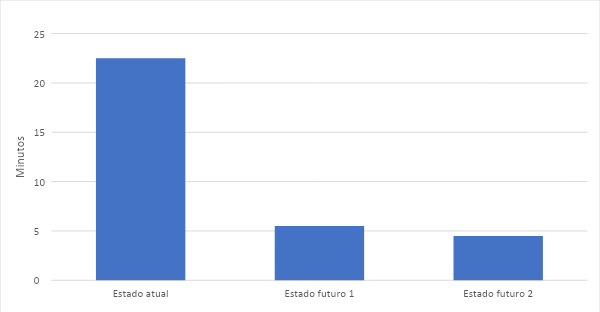
Resultado final
As análises e melhorias foram realizadas durante uma semana e contaram com a participação da operação para melhorar os processos e obter ideias e melhorias. Na segunda semana, foram realizadas as mudanças de tubulação e conexões. Com isso, o tempo prático foi reduzido de 22:00 minutos para 4:30 minutos. Para garantir que o novo tempo fosse mantido, foi confeccionado um treinamento para todos os operadores e criado trabalho padronizado para cada uma das etapas.
O maior problema era a falta de conexões e alinhamento de atividades para manter o fluxo, e com isso pequenas paradas e ausências impactavam na produção diária. Adotando a mudança na atuação de cada pessoa ao longo do fluxo, disponibilizando os recursos necessários para os operadores e fazendo um baixo investimento para melhorar os pontos de envase, foi possível quadruplicar o volume produtivo.
Entre em contato conosco para juntos conseguirmos aumentar a produtividade e conte com nossa equipe de consultores.
Por Adionil Jose Fumagali Junior
Consultor Sênior Lean