Durante as minhas visitas às fábricas, vejo com muita frequência um acúmulo de materiais dentro da área produtiva. Apesar da clara evidência do desperdício gerado por existir uma quantidade de estoque maior do que a necessária, gostaria de destacar outro grande desperdício ligado a esta situação, que muitas vezes fica esquecido. Trata-se do movimento do operador, que muitas vezes caminha durante o dia para pegar o material de que necessita, localizado dentro da área produtiva, porém distante de seu posto de trabalho. É com essa perspectiva que vou apresentar três passos e algumas técnicas para aumentar significativamente a produtividade do processo.
Um tema que sempre apresento em meus treinamentos é o conceito de “cirurgião”. Esse termo faz uma analogia com o que acontece nas salas cirúrgicas, onde o médico (que exerce a função mais importante) recebe imediatamente todos os materiais e instrumentos de que necessita. Na produção, deve acontecer a mesma coisa: o operador deve agregar valor ao cliente, ou seja, todo o seu tempo deve ser aproveitado para realizar uma transformação de matéria-prima, para o semi-acabado e para o produto final embalado.
Para que isso ocorra, devemos projetar o que chamamos de “ponto de uso”, que é composto pela área onde o material fica estocado e a área de trabalho do operador (também chamada de área de agregação de valor), e também como o material deve ser transportado.
1 – Como deve chegar o material:
Defina primeiramente a maior frequência possível de abastecimento dos materiais produtivos, utilizando o conceito de rotas e trens logísticos internos para otimizar esse processo. Espera-se como referência um abastecimento a cada 60 minutos. A frequência estabelecida permitirá a definição da quantidade de estoque no ponto de uso, que será igual à média de consumo multiplicada por três vezes o tempo da frequência de abastecimento.
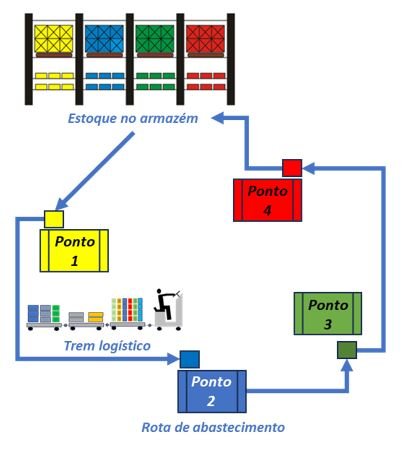
2 – Como armazenar o material
Antes de definir como o material deverá ser armazenado, devemos definir o tipo de abastecimento (kanban – ter estoque de todos os itens) ou (junjo – um kanban sequencial). Após definir o tipo de kanban, armazene o material o mais próximo possível do alcance do operador, deixando o material mais frequente mais perto. De preferência, coloque o material na frente do operador (abastecimento frontal) ou ao lado (abastecimento lateral). Utilize flow racks para facilitar o abastecimento e a retirada das caixas. Utilize o abastecimento frontal de pequenos contêineres sempre que possível com racks FIFO (primeiro que entra, primeiro que sai). Utilize o abastecimento lateral das caixas ou carrinhos somente quando o frontal não for possível. Também podem ser usados carrinhos que já foram pré-preparados no armazém. Neste caso, o abastecedor retira o último carrinho utilizado e o abastece com o novo.
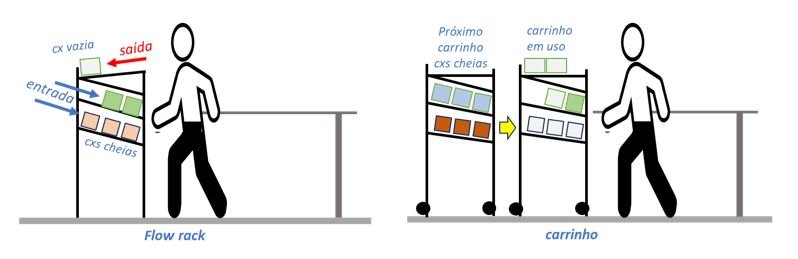
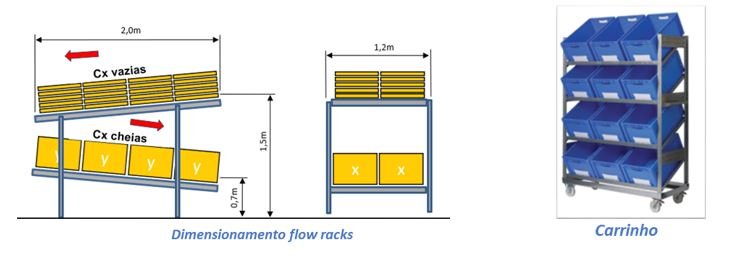
3 – Como organizar a área de trabalho
Deixe os materiais ao alcance do operador, sempre colocando os de maior frequência mais próximos. Se houver muita variedade de itens, utilize vários níveis de altura. Para facilitar a pegada do material, deixe as peças orientadas dentro da caixa e não se esqueça de fazer uma análise ergonômica para evitar a fadiga do operador.
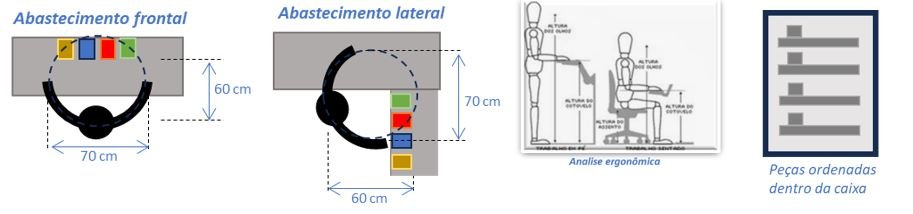
Utilizando essas técnicas, que normalmente têm um baixo investimento, é possível obter de 20% a 50% de aumento na produtividade através da eliminação do desperdício de “movimento”. Se ficou interessado e quer saber mais sobre o tema, entre em contato conosco e não deixe de seguir a 2blean para ter acesso a todo o nosso conteúdo.
Walter Cruz
Consultor Sênior