O que ocorria
Durante as mudanças e melhorias realizadas em um site do segmento agro de separação de sementes de milho, foi identificado, na análise desse processo e no mapeamento do fluxo de valor, atrasos no atendimento programado de manutenção, impactando a produção, além de uma grande quantidade de itens na área de manutenção. Com isso, foi planejado um trabalho para revisar todo o processo de manutenção deste site.
Problema encontrado
Durante as investigações, encontraram-se problemas de identificação e organização dos materiais, além de variação na quantidade de materiais armazenados utilizados. Além disso, o processo de solicitação e registro de manutenção não era claro e organizado, dificultando o planejamento da manutenção programada e o atendimento a quebras que impactavam na parada do fluxo produtivo.
Solução adotada
A primeira ação realizada foi o mapeamento do processo de manutenção, adotando a metodologia de mapeamento do fluxo de valor para processos administrativos. Com isso, o processo desde a solicitação da manutenção até a solução do problema foi clarificado e simplificado. Segue um exemplo abaixo:
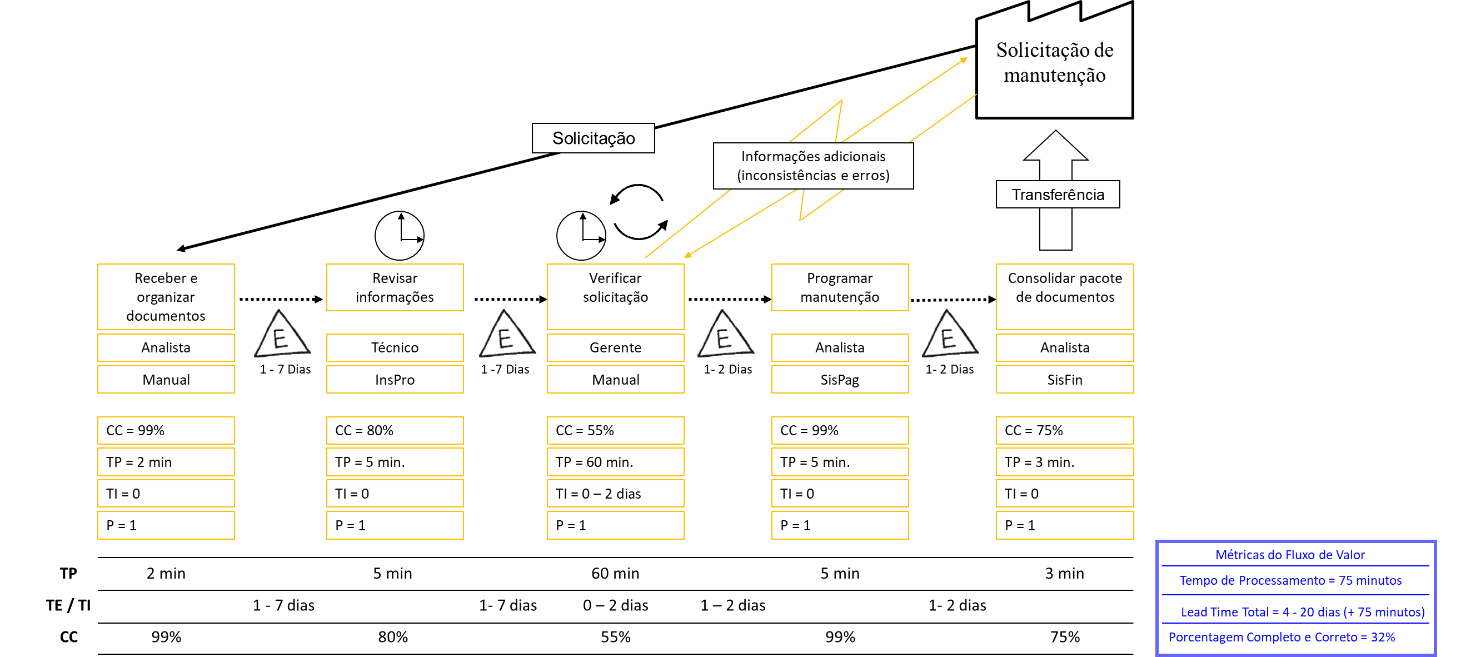
Em seguida, foram criados quadros para facilitar o acompanhamento dos atendimentos à fábrica, concebido um processo específico para manutenções corretivas e preventivas, e colocados indicadores para facilitar o acompanhamento da evolução e melhoria deste processo.
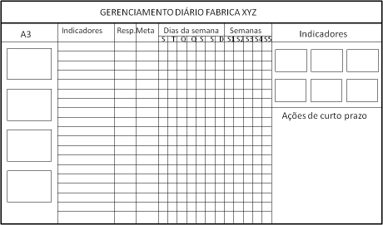
O próximo passo foi a revisão dos itens armazenados que atendiam o processo de manutenção. Foi criado um time de trabalho e identificados os itens de alto volume, baixo volume e esporádicos em relação ao consumo. Para cada um destes grupos e de acordo com a criticidade e tempo de reposição, foram recalculadas as quantidades de cada item adequadas para atender com segurança à produção. Nesta avaliação foram encontrados muitos itens obsoletos, danificados e também outros com excesso de material. Assim, foi realizado um plano para venda ou consumo, e obteve-se o nível adequado de materiais.
As etapas anteriores auxiliaram e apoiaram a padronização de itens e o descarte de materiais obsoletos/danificados. Com isso, foi revisada a organização e identificação dos materiais de acordo com este novo método. O custo total encontrado de materiais de manutenção inicialmente era de R$ 1.700.000,00.
Resultados obtidos
O primeiro grande resultado encontrado foi o melhor atendimento à produção. Com isso, ficou claro para toda a empresa o modelo de atendimento para manutenção corretiva e preventiva, impactando no aumento da disponibilidade do site. O segundo grande resultado foi com a revisão dos itens armazenados e disponibilizados para manutenção de acordo com a criticidade e volume adequado para atendimento ao processo produtivo. Esta revisão reduziu o valor de materiais de manutenção para R$ 950.000,00, ou seja, uma redução de 44% no valor de materiais armazenados, e agora redimensionados e adequados à necessidade de atendimento aos processos produtivos.
Se você se identifica com este caso relatado, entre em contato e conte com a ajuda de nossos consultores para obter um impacto significativo no processo de atendimento da manutenção à fábrica e redução do valor dos itens armazenados para atendimento à manutenção.
Por Adionil Jose Fumagali Junior
Consultor Sênior Lean