Nas melhores lembranças da sua infância, você provavelmente consegue se recordar de uma mesa cheia de coisas gostosas da vovó ou de um café da manhã com a família. Em meio a essas memórias, diversos produtos marcavam presença nas mesas, trazendo uma sensação saudosista inexplicável. Se você lembrar de algum produto térmico que acompanhava essas reuniões familiares, provavelmente virá à sua mente a marca Aladdin. Esses produtos são fabricados pela PMI, a empresa que projeta e fabrica produtos térmicos das marcas Aladdin e Stanley, tais como garrafas térmicas, cantis térmicos, jarras térmicas e produtos térmicos das linhas de cerveja, hidratação e camping.
A PMI fabrica as marcas de produtos térmicos que mais estão presentes na memória afetiva dos brasileiros. Com uma tradição de mais de 80 anos e duas fábricas, uma localizada em Manaus e outra em Cariacica, a empresa recentemente deu início a uma transformação lean em sua unidade de Cariacica, no Espírito Santo. Vamos conferir como está sendo o início da jornada na empresa.
Visando aprimorar suas entregas, a diretoria decidiu aplicar a filosofia lean na logística, pois havia alguns gargalos para entrega de produtos. O espaço para expedição era limitado, e a produtividade da operação era abaixo do esperado. Não havia muitos recursos tecnológicos na época e nenhuma automação de processos, o que tornava o processo de separação, conferência e expedição bem lento e complicado.
Iniciando a transformação:
Para iniciar a transformação, foi criada uma equipe multifuncional com a participação de 100% das pessoas da logística, produção e recursos humanos, que receberam um treinamento introdutório sobre lean aplicado à logística. Esse tema era novo para a maioria das pessoas, pois elas estavam acostumadas com a aplicação do lean somente na manufatura.
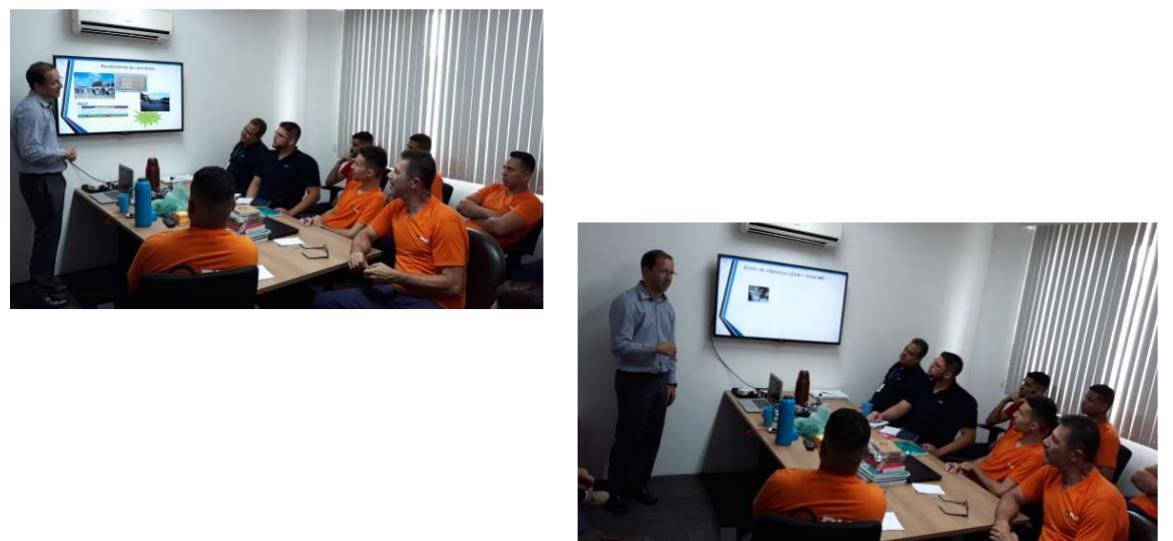
Foto da equipe recebendo treinamento
Nesse momento, houve uma quebra de paradigmas: existe uma diferença física muito grande entre a logística e a produção, o que cria bloqueios no entendimento dos conceitos lean aplicados à logística. Entre esses bloqueios está o fluxo contínuo, em que cada processo é balanceado para funcionar no conceito de “fazer um e mover um”. As pessoas normalmente têm dificuldade de enxergar isso na logística, pois os movimentos são feitos em paletes com grandes quantidades de produto.
Como a primeira atividade prática, a equipe desenhou o mapa de fluxo de valor logístico, desde a entrada do pedido até a expedição para o cliente final, e apontou os principais desperdícios. Entre os pontos principais que passaram a enxergar como problemas estavam:
1 – Excesso de caminhada na separação de produtos.
2 – Excesso de caminhada na conferência para procurar os itens separados, que ficavam espalhados na plataforma e em corredores distintos.
3 – Falta de produtos no ponto de acesso (parte inferior do palete) durante a separação.
4 – Muita anotação manual, o que possibilitava erros.
5 – Fila de caminhões aguardando o carregamento.
Desenhar o mapa de fluxo logístico foi uma maneira de enxergar o processo de uma forma diferente. Contudo, enxergar os desperdícios e considerá-los anormais foi um grande desafio, pois sempre surgia aquele tradicional comentário do “sempre fizemos assim”; veja como ficou o mapa atual:
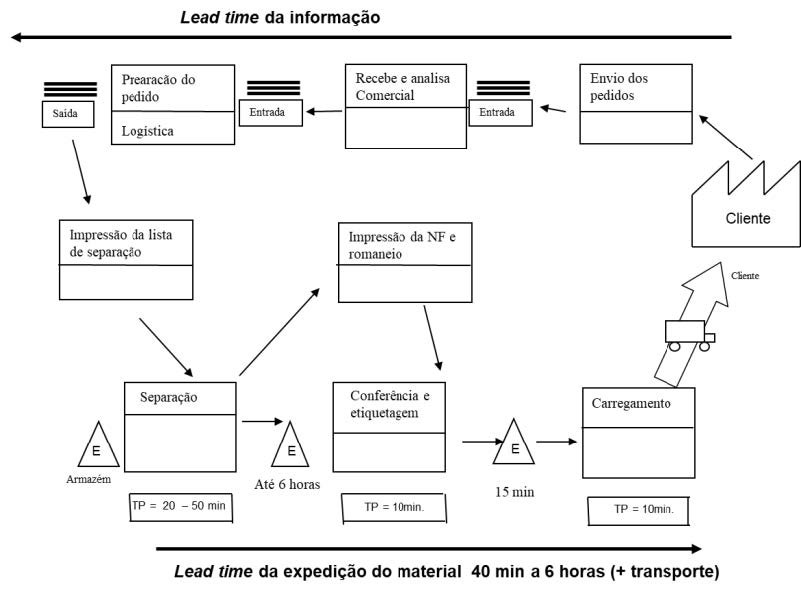
Figura do mapa de fluxo logístico
Desenhando o novo processo
Para que pudessem desenhar o novo processo, foi necessário que conhecessem os conceitos lean que poderiam ser utilizados para resolver os problemas identificados. Entre esses conceitos, podemos destacar:
Kanban – palavra japonesa que significa sinal, o kanban permite que o consumo de um determinado produto seja sinalizado para o processo fornecedor para que seja reposto assim que for consumido. Essa foi uma das ferramentas que a equipe usou para resolver o problema de reposição dos produtos na área de separação. Para isso, eles criaram um cartão vermelho e o colocaram no palete; quando o nível e as caixas chegavam ao último nível, os separadores avisavam o empilhadeirista para a reposição, evitando, assim, que o separador ficasse aguardando a reposição do produto.
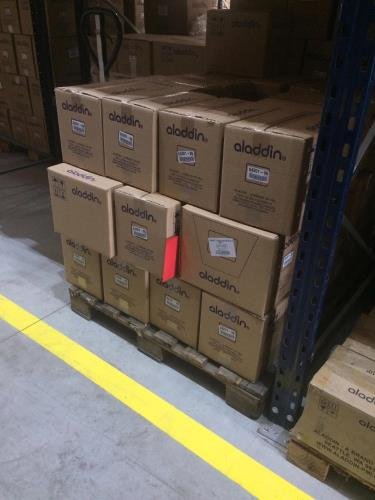
Figura do kanban vermelho no palete para indicar quando deve haver abastecimento
Diagrama de espaguete – esta ferramenta foi usada para mostrar a caminhada do operador e para enxergar os desperdícios de caminhada. A quantidade de passos do operador era anotada, e a caminhada dele era especificada. Essa ferramenta rendeu aprendizados incríveis, pois permitiu a descoberta de que o operador chegava a caminhar 600 metros por separação, um valor excessivamente alto. A partir dessa ferramenta, foi possível reposicionar os produtos para facilitar a separação, conforme é possível observar na figura abaixo.
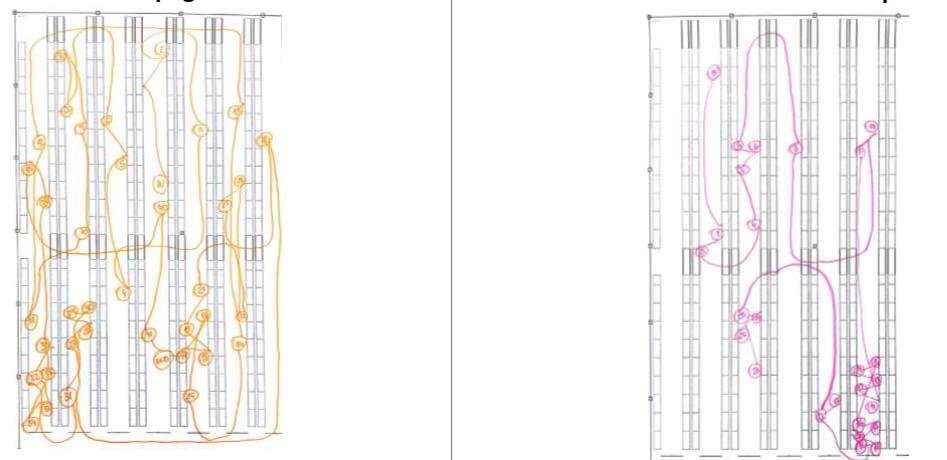
Figura do espaguete na separação – antes e depois
Fluxo Contínuo – este conceito significa “fazer um e mover um” em um fluxo sem interrupção e de forma que o operador não caminhe longas distâncias, ou seja, o que podemos fazer para aproximar os produtos para facilitar a separação? Com esse conceito em mente, a equipe fez uma análise do consumo dos produtos e identificou aqueles que tinham mais saída, colocando-os próximos uns aos outros e formando o que chamamos de célula (eles deram o apelido carinhoso de “feirinha” para a célula). Com essa configuração, houve uma redução de 30% na caminhada do operador.
Agendamento em fluxo – um dos conceitos que bastante trabalhado na logística foi o agendamento. Apesar de ser uma ferramenta simples, ela é infelizmente pouco utilizada. Com ela, torna-se possível nivelar a operação e evitar sobrecarga e desperdício, o que é muito comum na logística. Os caminhões chegam na mesma hora, gerando fila na entrada da empresa e na doca de expedição. No caso da PMI, foi criado um agendamento em que cada caminhão tem um horário específico para carregamento, evitando, assim, a fila e a sobrecarga da equipe de conferência.
Conferência em Fluxo – outro conceito que foi trabalhado fortemente na PMI foi o da conferência em fluxo. Sempre que possível, a conferência deve ser realizada em fluxo com a separação, o que evita o desperdício de espera. Nesse caso, eles trabalharam para que o separador fizesse a separação por transportadora; assim que ele terminasse um palete, o conferente imediatamente realizava a conferência, evitando que ela acontecesse somente ao final da carga separada.
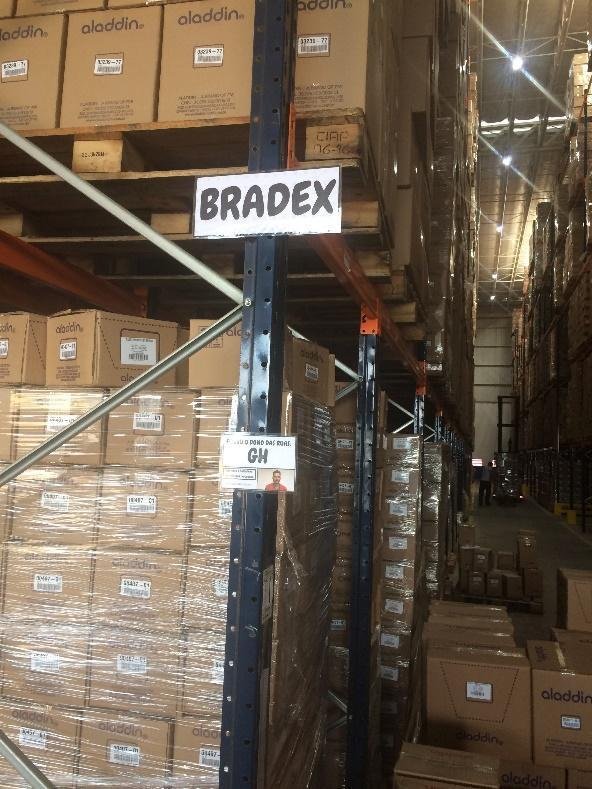
Foto do corredor com identificação do transportador e do dono da rua
Dono da rua – Este conceito de dono da rua permitiu que o 5S fosse implementado e mantido pelos separadores, pois eles passaram a se sentir donos da área que trabalhavam e exigiam aos demais que mantivessem organizado o local de trabalho.
Trabalho padronizado – Uma das ferramentas mais importantes da filosofia lean, o trabalho padronizado assegura que as melhorias não regridam. É a partir dele que descrevemos os elementos de trabalho, seu tempo e a movimentação do operador. Dessa forma, asseguramos que todos executem a tarefa da mesma forma, garantindo, assim, o resultado final do processo.
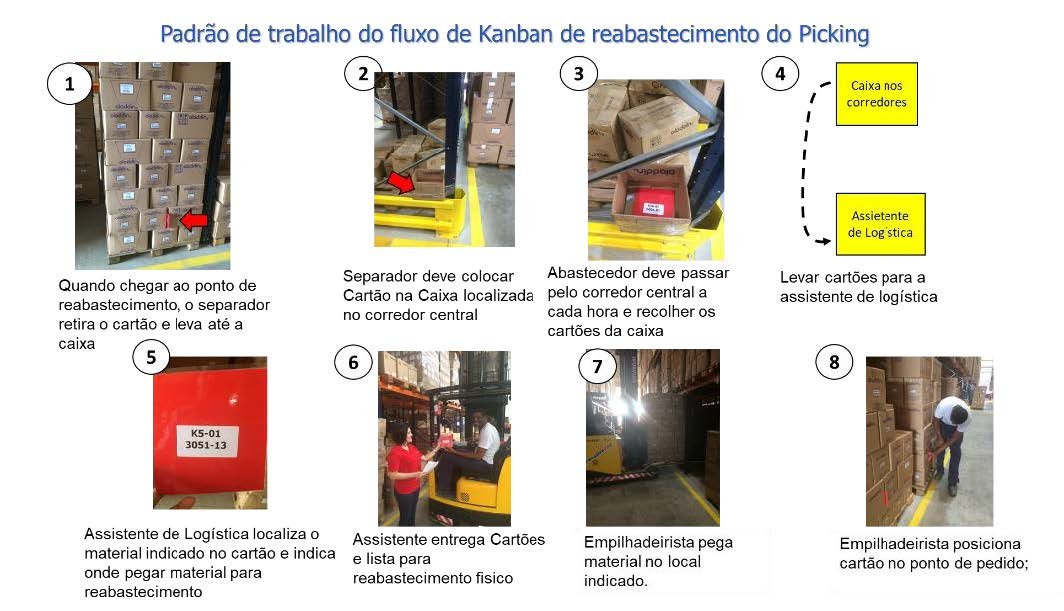
Figura do trabalho padronizado do reabastecimento
Após o entendimento dos conceitos, a equipe desenhou o estado futuro a ser implementado e um plano de ação, que foi consolidado no relatório A3. A implementação não foi fácil, mas a equipe estava disposta a mudar os conceitos. Com muita dedicação, eles implementaram a maioria das ideias, e aquelas que não foram possíveis ficaram para serem avaliadas mais adiante.
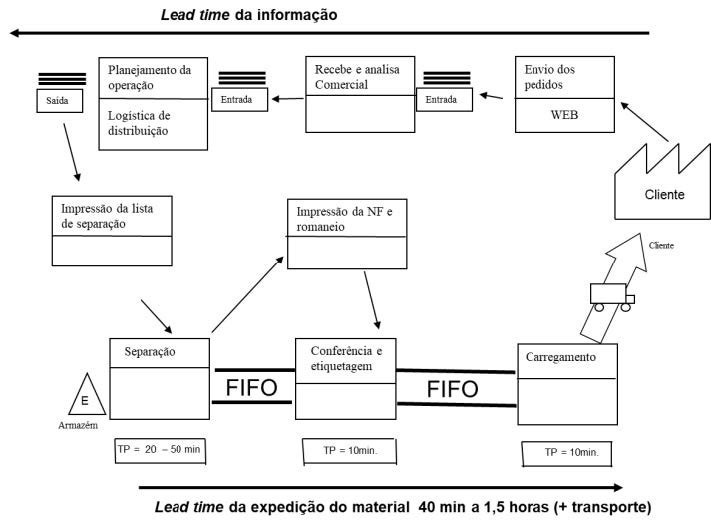
Figura do mapa de fluxo futuro
Criando um sistema de gestão na logística
Acreditamos que implementar apenas as melhorias nos processos não é suficiente. Para tornar perene as mudanças, é necessária a criação de um sistema de gestão que sinalize os problemas para que a gerência possa ajudar os operadores no seu dia a dia. Então, apoiamos a empresa a criar um sistema de gestão diária, com quadros de gestão à vista e reuniões sistemáticas para que os processos fossem visitados todos os dias para assegurar que as melhorias não regredissem.
Foi criado um quadro de gestão diária com os principais indicadores estabelecidos, que eram monitorados diariamente pelo gestor e pela equipe. Em verde, eram apontados os que estavam dentro da meta, e em vermelho, os que estavam fora da meta. Certamente, eles abriam um processo de análise sempre que algum indicador ficava dois dias consecutivos no vermelho.
Com essas reuniões, foi possível estimular a participação de todos na melhoria dos processos.
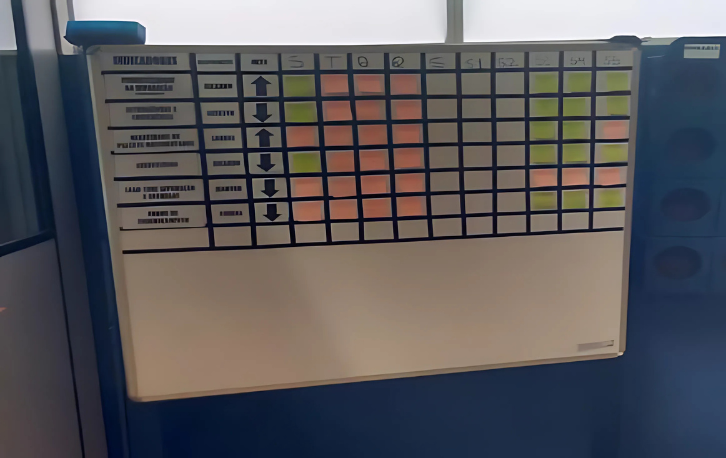
Figura do quadro do GD
Os resultados e os aprendizados
A transformação lean está apenas no começo, mas com resultados muito relevantes para a empresa e para as pessoas que participam do processo. Os principais aprendizados foram:
1 – Trabalho em equipe: As pessoas passaram a entender a importância de trabalhar em conjunto para enxergar todo o processo e exercer suas funções de forma colaborativa, a integração entre os separadores, conferentes e administrativo foi um dos principais aprendizados.
2 – Manter a mente aberta para as mudanças e acreditar nas propostas: para aceitar a filosofia Lean é necessário estar com a mente aberta, fazer experimentos para entender as novas ideias e acreditar que é possível mudar, a equipe se mostrou aberta a novas ideias, o que facilitou muito a implementação. Como dizia Taichi Ohno “Use a cabeça antes de usar o bolso”, famosa frase onde ele enfatiza novas ideias ao invés de usar muito dinheiro.
3 – Experimentação antes da implementação: Este é um dos conceitos mais importantes que deve ser praticado por todos, nunca descarte as ideias antes de testar, esta é uma forma de materializar as inovações que são imaginadas pelas pessoas, algumas não vão dar certo, mas a maioria se concretiza após a experimentação.
4 – O apoio da alta administração foi fundamental na transformação: Na PMI o apoio da Alta administração foi incondicional e possibilitou a implementação rápida das ideias, e vale ressaltar que o Vanderlei, Gerente da Unidade de Cariacica, apoiou e participou de todo o processo de transformação Lean, um verdadeiro líder lean que apoia e participa de tudo sempre incentivando a testarem novas ideias.
Os resultados atingidos no processo inicial foram:
- Ganho de produtividade entre 20 e 30%.
- Redução no tempo de carregamento de até 6 horas para 1,5 hora (pior caso).
- Redução na caminhada do separador em 20%.
Conclusão
Com essa experiência que tivemos, podemos afirmar que é possível fazer a transformação lean com o mínimo de investimento financeiro e utilizando o máximo das pessoas, com suas ideias simples e fáceis de implementar. Neste caso não tivemos nenhum investimento tecnológico, por restrições do negócio naquele ano, o que mostra que é possível fazer melhorias significativas no negócio aplicando os conceitos lean de maneira prática e eficiente. Veja como você pode implementar essa transformação lean nas suas operações logísticas seguindo os seguintes passos:
1 – Treine a equipe.
2 – Desenhe o mapa de fluxo logístico.
3 – Aplique os conceitos da logística lean.
4 – Desenhe o estado futuro.
5 – Elabore um plano de implementação.
6 – Crie um sistema de gestão.
7 – Apoie as pessoas da sua equipe na transformação lean.
Caso você precise de ajuda, conte com a 2blean!
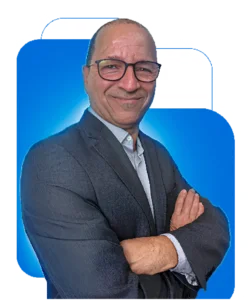
Por Alexandre Cardoso
CEO da 2blean – Especialista em Lean Thinking com mais de 25 anos de vivência prática, gerencia projetos de implementação dos conceitos em grandes empresas dos setores de alimentos, químico, automotivo, metalúrgico, consumo e de serviços. Desenvolve materiais e ministro treinamentos relacionados ao lean nas áreas de operação, logística e vendas para empresários e gestores. Mestre em Gestão da Produção pela Escola Politécnica da USP, Especialista em Lean Leadership pela Universidade de Kentucky EUA e Instrutor Internacional de TPM nº446 pelo JIPM. Autor dos livros: Uma vida sem desperdício – aplicando lean no dia a dia e Logística Lean em Centros de Distribuição.