Um dos grandes desafios das empresas de varejo no Brasil é a entrega na última milha, muitas enfrentam dificuldades com seu transportador ou entregador que faz a entrega para o cliente, muitas vezes as entregas não chegam no prazo prometido e muitas vezes não localizam o cliente final.
Este caso é sobre uma operadora logística, a Lean Express, que atua em Vitória da Conquista, uma pequena empresa cujo propósito é ser eficiente na entrega e oferecer um nível de serviço superior para a região, e para isso decidiu aplicar o lean nas suas operações antes mesmo de começar a entregar para seus clientes finais.

Foto da marcação no piso
O gestor da empresa já havia recebido alguns treinamentos de lean, e preparou sua operação de forma visual, com marcação no piso, definindo um lugar para cada coisa, com uma lógica que facilitava a separação para entrega ao cliente, recebeu treinamento antecipado do sistema do Cliente que iria entregar os pacotes para entrega e treinou sua operação. Até que chegou o grande dia de iniciar as operações, grande surpresa, ao receber os pacotes o gestor percebeu que os mesmos vinham misturados e que teria que organizar os mesmos antes de separar por região, além de distribuir os materiais por rotas.
Ao realizar as primeiras entregas percebeu que precisaria se organizar e entender melhor o processo, decidiu então fazer o mapa de fluxo de valor com o apoio da 2blean, empresa de consultoria localizada em Campinas, mas ele imaginou que a distância entre a consultoria e a empresa iria inviabilizar os trabalhos, foi aí que descobriu que a 2blean oferecia uma consultoria de logística Lean online onde o consultor não precisaria ir até a empresa para fazer o suporte necessário. No começo o gestor não acreditou muito, pois lean acontece no Gemba, e como o consultor ia ajudar sua equipe estando a quilômetros de distância da operação?
É ai que entra a tecnologia, o sistema utilizado pela 2blean permitia uma implementação da transformação lean levando o Gemba até o consultor, e não o contrário, com o uso de vídeos e simulações foi possível dar o suporte necessário para transformar a empresa, mas vamos ver como isso aconteceu!
A Jornada de Transformação
O principal problema que a empresa enfrentava era o tempo elevado de preparação das cargar para os motoristas entregarem os pacotes ao cliente final, e outra dificuldade era que o caminhão que trazia os pacotes não tinha um horário certo para chegar, podia chegar às 8 ou às 11, o que atrasava a saída dos motoristas, e estes problemas ficaram claros quando fizemos o mapeamento do fluxo logístico da operação.
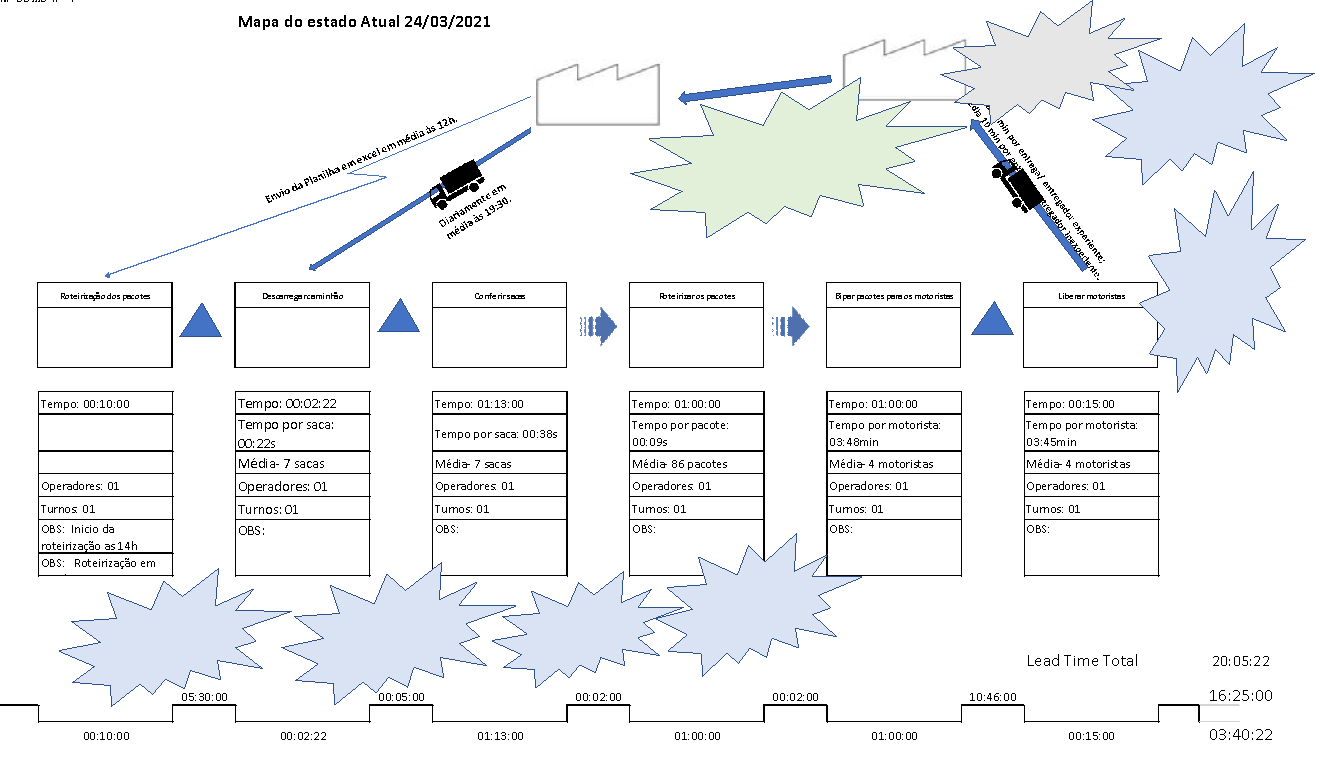
Figura do Fluxo de valor original (Tempo de operação = 3h40min – 447 pacotes Lead Time total= 20hs5min)
Mapeamento foi feito pela própria equipe após assistir a um treinamento online sobre mapeamento, com o suporte do consultor via remoto e acompanhando a filmagem que foi carregada no sistema da empresa consultora.
A primeira etapa da operação era descarregar o caminhão, o que não levava muito tempo, pois os pacotes vinham em sacas fáceis de descarregar. A segunda atividade era a conferência da quantidade de sacas e dos lacres de cada uma para verificar que nenhum havia sido violado.
Após liberar o caminhão, a operação tinha que conferir o que tinha em cada saca e endereçar nos paletes pré-determinados por região da cidade. Essa era a parte mais demorada, pois os pacotes vinham misturados e era necessário ler o endereço de cada pacote para identificar o bairro antes de fazer a leitura no sistema do cliente; nessa etapa, o tempo chegava a até 4 horas, dependendo do volume, é claro.
Para realizar essa etapa, a equipe tinha que retirar os pacotes da saca e colocar em algumas caixas para ordenar por bairro, para somente depois fazer a leitura do pacote no sistema e atribuir ao motorista que fazia a entrega. Após essa tarefa, ela colocava o pacote de volta na caixa para levar até a posição palete, deixando o pacote no local para o motorista retirar.
Outra atividade que era realizada pela administração era a roteirização, que era realizada pelo Excel, atribuindo cada pacote a uma rota específica, antes mesmo do pacote chegar. Dessa forma, ficava mais fácil para o motorista saber que pacote entregar em cada endereço.
Identificamos nesse processo vários desperdícios: movimentação excessiva – caminhada pela área para colocar os pacotes nos paletes –, processamento desnecessário – tirar da saca, colocar na caixa, tirar da caixa, colocar na caixa e colocar no palete –, espera – enquanto o caminhão não chegava, os motoristas ficavam esperando –, entre outros.
Identificando os kaizens para eliminar os desperdícios
Com o treinamento sobre lean e sobre os conceitos de fluxo contínuo, realizados online, e mais uma vez com o suporte do consultor, a equipe realinhou os paletes para facilitar o abastecimento, usando, inclusive, um carrinho para melhorar a distribuição, além de colocar um laptop para facilitar a leitura do código de barras do pacote para dar entrada no sistema.
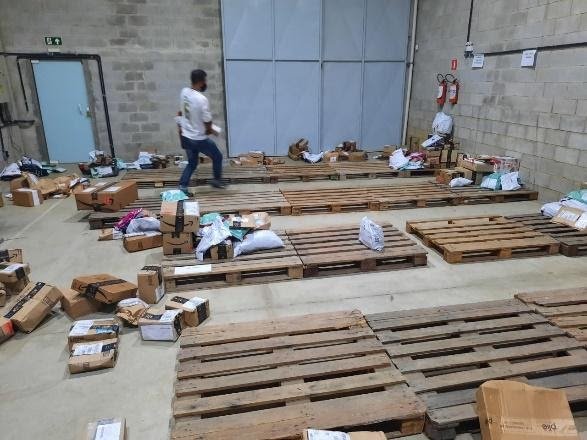
Foto com o novo layout de separação
Com isso melhorou um pouco o tempo, mas não o suficiente para eliminar etapas, foi então que o gestor da empresa (Alex Bernardino) teve uma ideia inspirada no que havia visto em outra empresa, a criação de colméias com rodinhas para evitar que o operador se deslocasse através dos paletes. A ideia foi um sucesso reduziu o tempo de separação em 70% e tornou a operação mais ergonômica para os separadores, na colmeia os pacotes são colocados na parte superior por região, e após a leitura do código de barras são transferidos para a parte inferior, prontos para os motoristas.
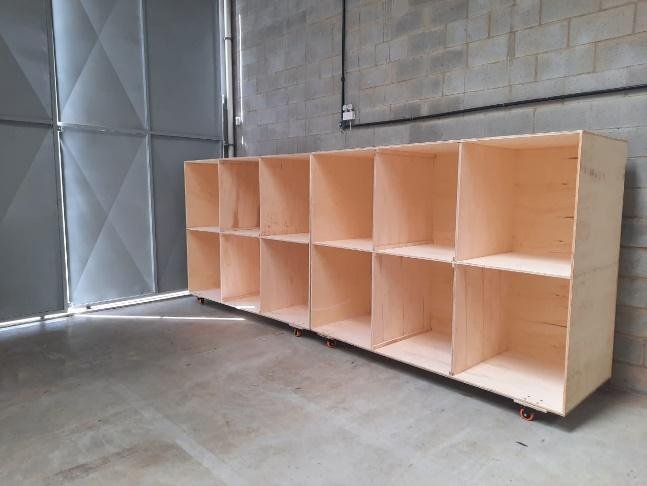
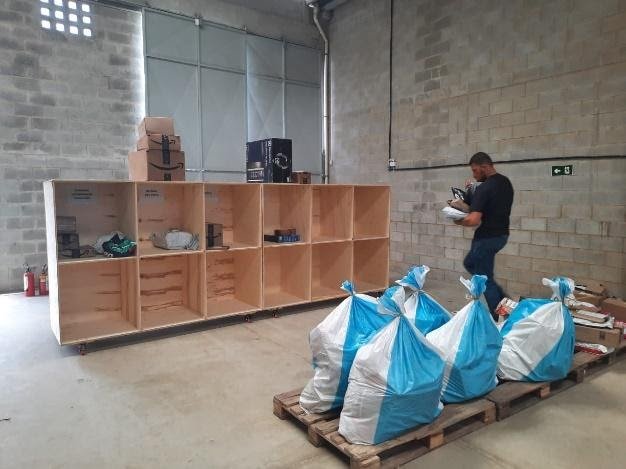
Fotos das Colméias
Contudo, ainda havia o problema da roteirização, algo que levava até 40 minutos para ser feito. Um dos consultores sugeriu que fosse criado um sistema no Excel de forma a otimizar esse processo a partir do arquivo que a empresa recebia do cliente. Colocamos a ideia em prática, e a 2blean desenvolveu uma macro no Excel para que, ao transportar os dados, levava-se apenas 5 minutos para fazer toda a operação, uma redução de tempo de 60%.
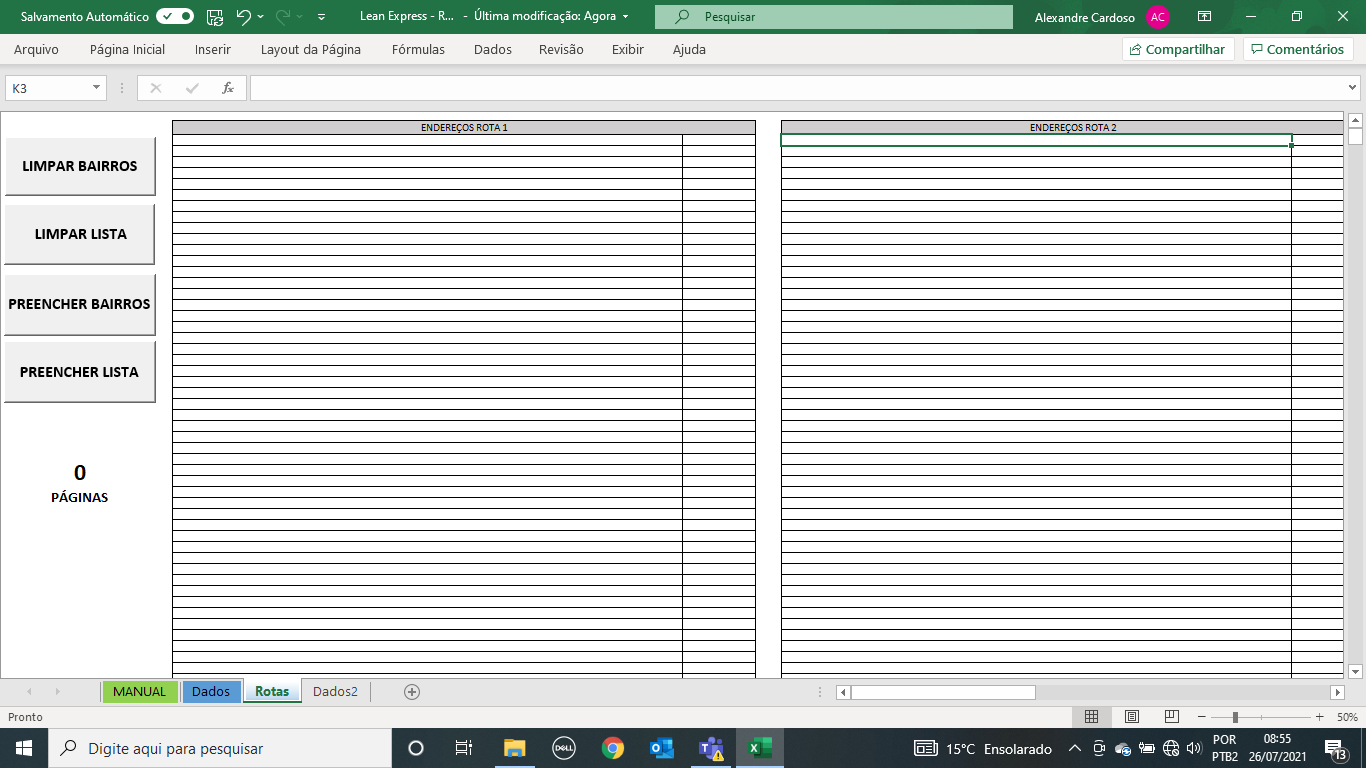
Bom, nesse ponto da jornada já havíamos atingidos ótimos resultados com as mudanças, mas ainda achávamos que podíamos melhorar; havia uma operação de identificação sobre qual bairro pertencia cada pacote, com a leitura sendo realizada etiqueta por etiqueta, lendo efetivamente o endereço para achar o bairro. Como isso interrompia o fluxo de trabalho do separador, a equipe, embasada em alguns exemplos de poka yoke que utilizavam o código de barra para evitar erros, pensaram se não seria possível fazer com que o computador, através do código de barras, especificasse o bairro. Para nossa sorte, temos um consultor que conhece bem de Excel, e ele disse que iria avaliar a possibilidade de criar algo que pudesse identificar o endereço; vale lembrar que essa empresa não tem um sistema de controle implementado e nem verba para isso, então tínhamos que fazer o que disse Taiichi Ohno: usar a cabeça antes de usar o dinheiro.
A consultora desenvolveu um pequeno sistema que, ao ler o código de barras do pacote, mostrava automaticamente o nome do bairro ao qual aquele pacote pertencia. Isso deu certo, e, com essa implementação, a atividade diminuiu muito o tempo, um ganho significativo.
Após essas melhorias, o processo hoje tem um tempo de operação de 55 minutos, sendo que o valor anterior era de 3h e 23 minutos, o lead time total ainda é elevado, pois a gestão decidiu iniciar o processo de separação somente após as 18:00 hs do dia anterior à entrega, gerando uma espera de até 10 horas para o motorista sair para a entrega, esta decisão se deve ao fato de que a entrega pela transportadora para a Lean Express ainda tem horários irregulares, o que geraria atrasos na entrega, e o fluxo de valor com os tempos atuais ficou assim:
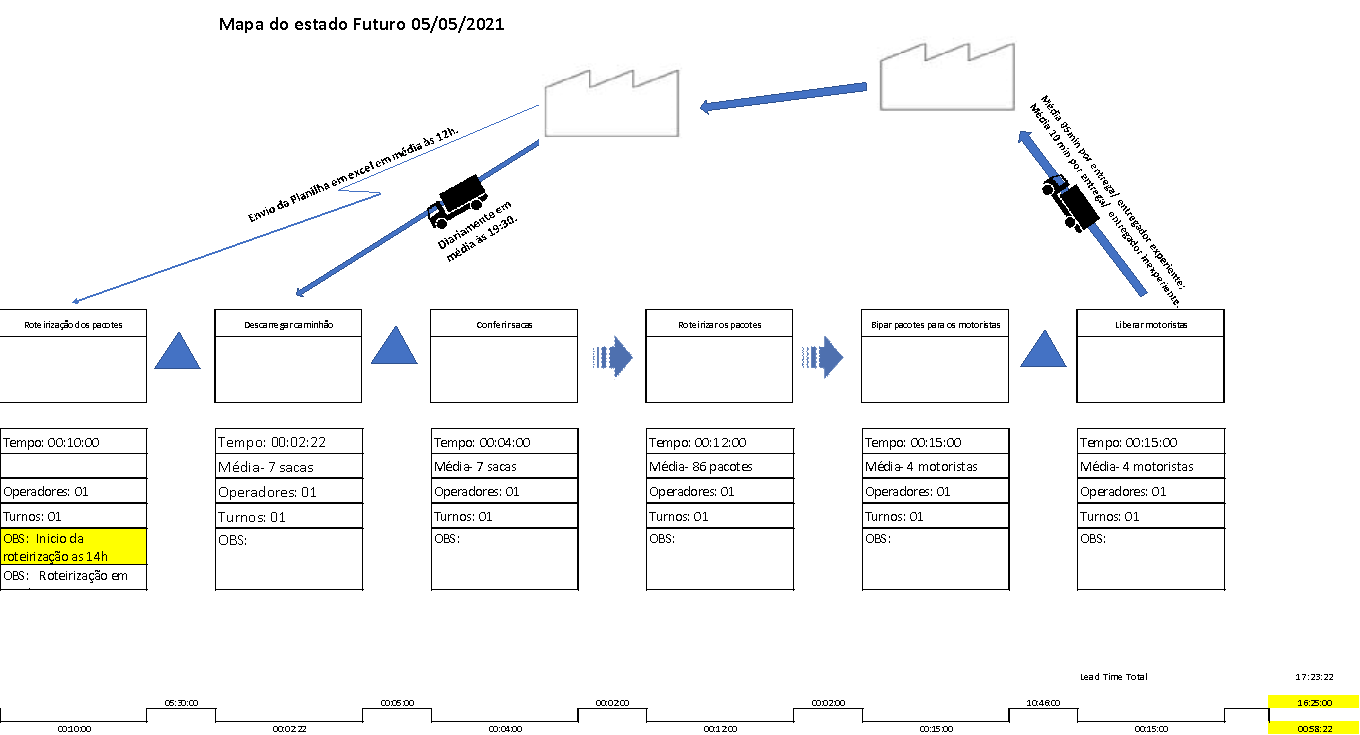
Figura do Fluxo de Valor após as melhorias
Resultados
A jornada lean apenas começou na empresa com o apoio da 2blean, mas já tem resultados interessantes em termos de tempo:
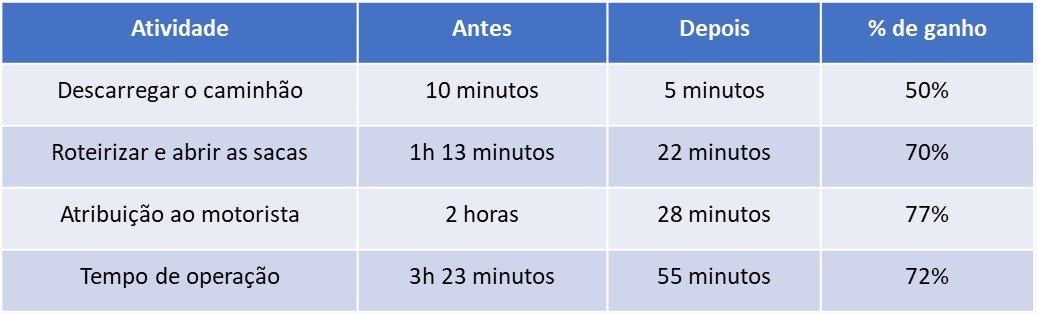
Conclusão
Com estas melhorias a Lean Express foi reconhecida pelo cliente como uma das melhores operadoras em termos de atendimento e pontualidade, e pudemos também mostrar que apesar da distância entre o consultor e a empresa é possível fazer a transformação com o uso da tecnologia para encurtar as distâncias físicas. A Logística Lean Digital rompe barreiras e torna possível que pequenas empresas também podem evoluir na jornada lean.
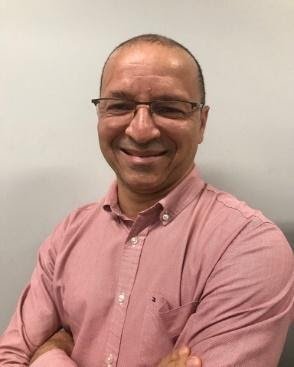
Alexandre Cardoso – Presidente da 2blean (www.2blean.com.br). Especialista em Lean Thinking com mais de 25 anos de vivência prática, gerencia projetos de implementação dos conceitos em grandes empresas dos setores de alimentos, químico, automotivo, metalúrgico, consumo e de serviços. Desenvolve materiais e ministro treinamentos relacionados ao lean nas áreas de operação, logística e vendas para empresários e gestores. Mestre em Gestão da Produção pela Escola Politécnica da USP, Especialista em Lean Leadership pela Universidade de Kentucky EUA e Instrutor Internacional de TPM nº446 pelo JIPM. Autor dos livros: Uma vida sem desperdício – aplicando lean no dia a dia e Logística Lean em Centros de Distribuição.
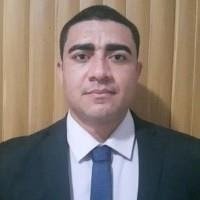
LEX BERNARDINO, Especialista em Logística Empresarial, com 20 anos de vivência prática em operações logísticas de distribuição. Em sua trajetória profissional, destaca-se por dirigir grandes operações logísticas com estabelecimento de uma forte cultura de excelência operacional através do Lean Manufacturing cujos objetivos principais são otimizar e padronizar processos, eliminar desperdícios e melhorar a produtividade com o objetivo de aumento da competitividade da organização. Possui M.B.A Executivo em Gestão Empresarial pela Fundação Getúlio Vargas (FGV), Especialização em Engenharia de Produção pela PUC-MINAS, dentre outros cursos já realizados nas maiores escolas de gestão e negócios do Brasil como: Fundação Dom Cabral, IBMEC, Falconi, Fundação Vanzolini, Lean Institute Brasil entre outras. Atualmente ocupa o cargo de Diretor de Operações da Lean Express Operador Logístico suportando melhorias de processos e aumento de resultados.
CONTATO: alex@leanexpresslog.com.br
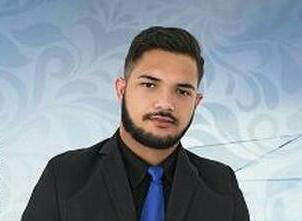
EDUARDO LUZ, Especialista em Melhoria Continua de Processos Logísticos, Graduado em Administração de Empresas, Pós Graduando em Gestão de Pessoas e Psicologia Organizacional. Desenvolveu por um longo período atividades em uma distribuidora do ramo de material elétrico e de construção com foco em redução de custos, gestão de inventário, desdobramento de metas, gestão orçamentária e desenvolvimento de projetos de melhoria contínua. Atualmente ocupa o cargo de Supervisor de Operações na Lean Express Operador Logístico, desenvolvendo atividades voltadas a gestão de contratos de transportes, performance operacional, projetos de consultoria em gestão empresarial e supervisão de toda cadeia de distribuição regional de transportes.
CONTATO: logistica@leanexpresslog.com.br